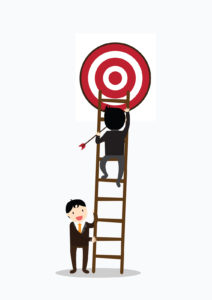
Wood, a global leader in the delivery of project, engineering and technical services to energy and industrial markets, thinks locally when it comes to workforce development and training. A relatively small project for the company in Georgia, requiring about 250 construction workers, is serving as a training test pilot for the company.
Led by Mittie Cannon, Manager of Workforce Development, the program takes advantage of relationships built between local workforce development councils, industry trade groups, community organizations, and nationwide training provider, Crane Industry Services LLC, which is headquartered near a current Wood project.
“Our greatest asset is our people,” said Cannon. “We were looking for a way to provide our employees with ongoing training and credentials, but there’s only so much you can do on the job site,” she said. Both Wood and CIS are NCCER-accredited training sponsors providing nationally recognized credentials. The two organizations will share an off-site facility to deliver skills training for craft professionals as well as leadership and team building training for front line supervisors. Since June 2017, the partners have been working together and realizing good results.
Training for electricians, carpenters, pipefitting, crane operation, and signal persons began just six months ago, and will conclude in the fall of 2018, although the scope of the project continues beyond that.
“Skills add value for life, to organizations and individuals,” said Debbie Dickinson, CEO of CIS. “This pilot training program is designed to ensure that a qualified, skilled workforce is available to meet our client needs.”
We asked Cannon, Dickinson, and Richard Campbell, a Piping Field Engineer who has 43 years of experience working for Wood and its predecessors, about their perspective on training and how Wood is implementing its pilot program.
What’s leadership’s perspective on training?
Cannon: “In 2016, our leaders recognized that employees were as concerned about training and workforce development issues as management was. Many companies view training only as a cost, but we want to create a culture that supports ongoing skills development. Providing employees with opportunities to gain advanced skills helps them feel appreciated.”
How has corporate culture changed regarding training and its perceived value?
Campbell: “Training used to consist of what you picked up while working with journeyman level workers. Through the years, there has been a reduction in journey level employees. Efforts to provide training on the job site often fizzled out. Today the need to educate our replacements in our industry has become a bigger concern. Upper management sees the need not only for more training, but to get more of our youth involved in learning a craft.”
How can employers make sure training is meaningful?
Campbell: “There has to be an end goal to encourage workers to strive for perfection. Employers should engage from the top down and employees need to know that management is supportive and willing to do what it takes to assist them in accomplishing their personal goals as a craft professional.”
What results do you expect to get from implementing comprehensive training programs?
Cannon: “Obviously a trained workforce is a safer workforce, but research has also shown that training contributes to improved productivity, quality, and employee attendance.”
What’s unique about the training you are providing?
Cannon: “We are not doing anything that hasn’t been done before, but we are taking a deliberate approach to deliver meaningful, robust training. We review the scope of work before we mobilize to identify any specialty training needed proactively, and we encourage employees to take advantage of the training available that expands their skill level.”
How many people do you expect to participate in training?
Cannon: “Our goal is 30% of the workforce to take part in training over the life of the project. We currently have between 40 and 55 percent engaged.”
How will you demonstrate that training is effective?
Cannon: “The corporate culture views training as an employee benefit. The percent of participation is one measure, and over a longer window we will be able to gather data on things like productivity, and accident reduction. But in the short term, we’ve had six laborers/helpers since June participate in training that advanced them to the next level. That means we have six people available internally with new skills we can use and we don’t have to go outside for those people. Even more have added new credentials, such as rigger or signalperson.”
Dickinson: “When employers go beyond compliance-only mentality and focus on training for skilled operations, safety increases and job delays and downtime decrease.”
What will improve the workforce outlook for the construction industry as a whole?
Cannon: “Contractors have to do a better job of establishing relationships in the local communities to create a pipeline of people coming into the industry. We must get involved in career and technical education, with local economic development groups, with faith-based organizations, and others.”
The Construction Leadership Initiative
/in Company News, Resources /by Tracy BennettMarket turns, sudden competitive or pricing pressures, mergers, acquisitions, key management turnover—any of these can throw even the best leadership teams off course. The consequences are rapid, and often brutal, resulting in lower productivity as the organization fumbles to get re-aligned on direction. This in turn creates a vacuum that is quickly and easily filled with competing priorities, inefficiency, and low employee morale. Without cohesive, current, and aligned strategies, the business becomes rudderless.
The Construction Leadership Initiative helps leaders align their business strategy with their people strategy from senior to middle management teams. This alignment promotes workforce commitment, which, in turn promotes business growth and positive transformation—and the ability to deliver the highest quality work in the quickest timeframe.
Additional topics
Start driving construction leadership excellence in your organization today. Learn More.
Contact Debbie Dickinson, Debbie@craneindustryservices.com, or Peter Krammer, krammer@elaconsultinggroup.com.
Robinson, Galloway Join CIS Team
/in Company News /by Tracy BennettFred Robinson
Shawn Galloway
As Crane Industry Services has expanded its training programs, workshops, and inspection services, two new staff members have joined the team—Fred Robinson, Business Relationship Manager and Shawn Galloway, Crane & Rigging Trainer.
Robinson brings decades of experience in business development and leadership managing complex government service projects. His primary responsibilities include helping CIS customers to receive optimal value from their CIS training. “Fred has a servant’s heart and is passionate about helping people do their job safely,” said Dickinson.
Galloway has more than 25 years of experience in Construction, Military, and Industrial sectors, and is cleared for work in safety sensitive areas. In addition, using his previous experience writing training protocols for unmanned aerial vehicle operations in the military, including drone tactical standards for the U.S. Army, Navy, Air Force, and Marines.
Galloway is applying this experience to the development of a Skills Measurement Record for simulators in crane training. “First, we identify the most common skills needed, and the most critical skills. We build scenarios for the simulator based on that and write curriculum, evaluations, and metrics to measure performance specific to the utility company’s training needs,” he explained. While the protocol would be customized to each employer and the skill level of employees, it provides a foundation for establishing how much simulator training is needed to achieve a certain skill level.
Crane Industry Services Moves to Larger Training Facility
/in Company News /by Tracy BennettCrane Industry Services, LLC (CIS) has relocated to a new larger facility that offers broader skills assessment and training programs to meet current business demands. The new Centered on Safety Training Center is located at 2692 Hwy. 27 N, Carrollton, Ga. The 8,892-sq. ft. facility is situated on about 3.5 acres of land, convenient to the Atlanta airport, West Georgia and Birmingham, Ala.
The new facility features multiple training rooms, an NCCER testing center, a simulation room, land for crane training and two warehouses for hands-on training. Previously the Centered on Safety Training Center was located on the West Georgia Technical College campus. “Our partnership with West Georgia Technical College continues, but this new facility allows us the space to now offer skills training in welding, electrical, millright, and carpentry, as well as rigging and crane operation,” said Debbie Dickinson, CEO of CIS. “While CIS’s expertise is skills training for workers in construction, energy, and heavy industrial markets, our sister company Instructional Dimensions and corporate partnership with ELA Consulitng Group, also provides executive leadership training and boot camps,” said Dickinson.
With the opening of the new facility, CIS can now offer assessment and training after hours and weekends to meet the needs of customers who must work training around job schedules.
Expanding Worker Skill Sets
/in Resources, Skilled Labor Supply /by Tracy BennettProvide employees a plan for ongoing development
“Forcing employees to learn their jobs on the fly can be extremely inefficient. . . take the extra day to teach them the necessary skills to do their job,” states the blog article on Zenefits’ website.
According to Zenefits: “Helping employees expand their skillsets contributes to a more advanced workforce. There are a number of ways you can support employee development: individual coaching, workshops, courses, seminars, shadowing or mentoring, or even just increasing their responsibilities. The results are employees who are more efficient and productive.
At CIS, trainers and inspectors have training and technical credentials and on-the-job experience. They understand how machinery works, from education, military training and or field experience. They can all operate equipment with proficiency. Our welders are experienced in steel erection. Our crane operators are certified. The skills are imperative, but just as important, is that our trainers understand their connection to our company strategy and the customer’s company strategy. Our employees know what folks working around them are doing, and they understand the challenges of each other’s trades.
Getting to this point means that we assess our employees for gaps in skills and provide them the tools to fill those gaps. That’s the same approach we encourage our customers to take. It’s a long-term approach to employee development.
Plant shutdowns and jobsite weather delays provide time in the schedule to take advantage of training. To make the most of it, be ready to conduct a thorough assessment of the skills gaps in the workforce, in the context of the company’s annual strategic plan. Here are a few tips for integrating strategic training and assessment in your operations:
Training that is directly related to organizational goals, and that improves the skills, safety, and productivity of workers, will be of far greater benefit to your operations in the long run than simply performing compliance-based training
Pilot Program Brings Together two NCCER Providers to Deliver Localized Training
/in Skilled Labor Supply /by Tracy BennettWood, a global leader in the delivery of project, engineering and technical services to energy and industrial markets, thinks locally when it comes to workforce development and training. A relatively small project for the company in Georgia, requiring about 250 construction workers, is serving as a training test pilot for the company.
Led by Mittie Cannon, Manager of Workforce Development, the program takes advantage of relationships built between local workforce development councils, industry trade groups, community organizations, and nationwide training provider, Crane Industry Services LLC, which is headquartered near a current Wood project.
“Our greatest asset is our people,” said Cannon. “We were looking for a way to provide our employees with ongoing training and credentials, but there’s only so much you can do on the job site,” she said. Both Wood and CIS are NCCER-accredited training sponsors providing nationally recognized credentials. The two organizations will share an off-site facility to deliver skills training for craft professionals as well as leadership and team building training for front line supervisors. Since June 2017, the partners have been working together and realizing good results.
Training for electricians, carpenters, pipefitting, crane operation, and signal persons began just six months ago, and will conclude in the fall of 2018, although the scope of the project continues beyond that.
“Skills add value for life, to organizations and individuals,” said Debbie Dickinson, CEO of CIS. “This pilot training program is designed to ensure that a qualified, skilled workforce is available to meet our client needs.”
We asked Cannon, Dickinson, and Richard Campbell, a Piping Field Engineer who has 43 years of experience working for Wood and its predecessors, about their perspective on training and how Wood is implementing its pilot program.
What’s leadership’s perspective on training?
Cannon: “In 2016, our leaders recognized that employees were as concerned about training and workforce development issues as management was. Many companies view training only as a cost, but we want to create a culture that supports ongoing skills development. Providing employees with opportunities to gain advanced skills helps them feel appreciated.”
How has corporate culture changed regarding training and its perceived value?
Campbell: “Training used to consist of what you picked up while working with journeyman level workers. Through the years, there has been a reduction in journey level employees. Efforts to provide training on the job site often fizzled out. Today the need to educate our replacements in our industry has become a bigger concern. Upper management sees the need not only for more training, but to get more of our youth involved in learning a craft.”
How can employers make sure training is meaningful?
Campbell: “There has to be an end goal to encourage workers to strive for perfection. Employers should engage from the top down and employees need to know that management is supportive and willing to do what it takes to assist them in accomplishing their personal goals as a craft professional.”
What results do you expect to get from implementing comprehensive training programs?
Cannon: “Obviously a trained workforce is a safer workforce, but research has also shown that training contributes to improved productivity, quality, and employee attendance.”
What’s unique about the training you are providing?
Cannon: “We are not doing anything that hasn’t been done before, but we are taking a deliberate approach to deliver meaningful, robust training. We review the scope of work before we mobilize to identify any specialty training needed proactively, and we encourage employees to take advantage of the training available that expands their skill level.”
How many people do you expect to participate in training?
Cannon: “Our goal is 30% of the workforce to take part in training over the life of the project. We currently have between 40 and 55 percent engaged.”
How will you demonstrate that training is effective?
Cannon: “The corporate culture views training as an employee benefit. The percent of participation is one measure, and over a longer window we will be able to gather data on things like productivity, and accident reduction. But in the short term, we’ve had six laborers/helpers since June participate in training that advanced them to the next level. That means we have six people available internally with new skills we can use and we don’t have to go outside for those people. Even more have added new credentials, such as rigger or signalperson.”
Dickinson: “When employers go beyond compliance-only mentality and focus on training for skilled operations, safety increases and job delays and downtime decrease.”
What will improve the workforce outlook for the construction industry as a whole?
Cannon: “Contractors have to do a better job of establishing relationships in the local communities to create a pipeline of people coming into the industry. We must get involved in career and technical education, with local economic development groups, with faith-based organizations, and others.”
Crane Industry Services Announces Simple Crane Operator Documentation Process for Employers
/in Company News, Employer Responsibility, Skilled Labor Supply /by Tracy BennettExample of a Skills Evaluation report produced for the QCOE. Exercises, written tests and practical exams are used to evaluate the qualification of a crane operator. CIS tracks the individuals and maintains records with recommendations for the organizations to improve ability and safety.
While employers have until November 2018 to make sure crane operators are certified, they currently have a duty to ensure crane operators are competent. (See current language presented in the OSHA Regulation update.)
To assist employers in evaluating and documenting crane operator competency, Crane Industry Services, LLC introduces a new and efficient process called Qualified Crane Operator Evaluations™ (QCOE). The process gives employers valuable insights not available in certification testing by identifying specific operator strengths and skills that need to be improved.
Competency is defined as one who is capable of identifying existing and predictable hazards in the surroundings or working conditions, and who has authorization to take prompt corrective measures to eliminate them. When it comes to crane operation that may entail familiarity with the type and configuration of the crane, hand signals, rigging, and ground conditions, among other factors.
The QCOE process graphs areas where knowledge and skill are strongest and where the operator and supervisors would benefit from more training or experience that the employer can provide or can be obtained through a reliable source. Employers receive recommendations for improved performance and documentation for current compliance requirements. The process lowers costs and hassles associated with certification testing.
Crane Industry Services travels to the crane and operator’s location to conduct tests and documents each operator’s qualifications. “Excuses don’t work when an employer is behind on a job schedule or over budget due to skill levels that are lower than needed to complete timely, quality, safe work. QCOE also helps employers fulfill the ‘employer duty’ to provide documentation to OSHA regarding qualification of operators, but the main benefit is safer, higher quality work,” said Debbie Dickinson, CEO of CIS.
Sample results tracking an individual’s record from novice to qualified crane operator. CIS has developed more than 200 exercises, many of which can be performed on a simulator, for demonstrating skills related to crane and lifting equipment operation.
CIS is WBE certified and NCCER accredited to train and provide OSHA recognized, ANSI accredited crane operator certification testing.