Crane Industry Services, LLC recently took delivery of a Vortex Edge Plus portable crane training simulator produced by CM Labs Simulations. To welcome the arrival of the new simulator, CIS hosted a demonstration event with CM Labs at the CIS Centered on Safety facility in Carrollton, Ga. The portable crane operations simulator garnered a lot of attention during the event, reports LD Stutes of CM Labs and Debbie Dickinson, CEO of Crane Industry Services.
In attendance were representatives from IUOE Local 926, Oak Ridge National Laboratory, the Georgia Department of Transportation, as well as regional and national construction and highway companies.
Since 2016, CIS has used a full-size simulator which is the forerunner to the Vortex Advantage, produced by CM Labs. The Vortex Advantage is an immersive training simulator with a plug-and-play training platform that is scalable to training needs and customizable to the crane fleet. In contrast, the new Vortex Edge Plus is designed for simple transport and set-up. “The desktop-style simulator is portable, making it easier for training organizations to bring simulator training to their clients’ locations,” said David Clark, content manager, CM Labs Simulators. “It is equipped to run any CM Labs training module, which includes mobile cranes, tower cranes, forklifts, and earthmoving equipment.”
“During the event, there was a lot of discussion about how expensive it is to train an operator,” said Dickinson. “With a simulator, one person can be trained much faster and more economically than in the cab of a crane.” The self-guided programs are progressive in nature, and capture operator metrics, for valuable feedback, explains Clark. CIS sends a simulator technician, who is also a certified instructor and certified crane operator, to set up the portable simulator in different locations. The instructor handles the technical side of the machine and can simultaneously coach the trainees. The simulator-based training reduces the man hours to train to a 3: or 4:1 ratio, and does not require job site supervisors or rigging crews for the training exercise, or valuable equipment time.
Demo event attendee Nathan Sauls, corporate health and safety director for Brooks Berry Haynie and Associates (BBH), an electrical contractor based in Mableton, Ga., said he can see many advantages to incorporating a simulator into crane operator training. For BBH, the biggest is in screening the qualifications of potential new hires. “I tried both the portable and permanent machines at the CIS event. I can see BBH, in the future, using that technology to set a baseline for hiring operators. It’s definitely got some good qualities for that purpose.”
He says it’s an expensive investment to hire personnel who may not have as much experience as they claim. Currently, BBH’s pre-hire screening involves comparing the skills of the potential employee to an operator they know is qualified. “It can be a financial drain if you spend money hiring someone and putting them in the field only to find out they’re not all they’re cracked up to be. With a simulator you can set a baseline on that good operator,” says Sauls.
Mark Templeton, business manager for the IUOE Local 926 in Rex, Ga., says training on the simulator is a realistic experience. “The motion, the seat moving around, giving you the effect of a real-life crane cab experience impressed me,” he said. “I’m a crane operator myself and the effect was realistic. We have a CM Labs simulator at the IUOE international training site and I’ve been able to get on it.” He believes the tabletop models are good for learning a crane’s functions, such as LMI readings, and better understanding the particular crane’s operations. “But the big system, that gives you the seat simulation, the movement and the motion, is dead on to what you’re going to get in the cab of a crane.”
A crane operator would pick up skills more quickly with a simulator, believes Templeton. “There are more things he can be aware of, and different skills that can be taught, in that situation,” he says, noting he’s spent 20 years in crane operations in the field and has worked around cranes of all types. “Your initial fears of being in a crane and the risks involved in operating heavy machinery—you take that risk factor out when you practice using a simulator, and you avoid the chance of damaging the equipment.”
Illustrating that point exactly, CIS reported that shortly after the CM Labs demo event, a customer utilized the cab-style simulator to prepare for a rough-terrain crane practical exam for crane operator certification. The operator had several months of job-related experience before starting the training. After spending about 40 hours on the Vortex simulator and 10 hours on an actual crane in the yard, the operator was able to pass the practical exam on the first try.
“Many trainees would require more time in the seat to pass the practical exam from the cab of a real crane, which further validates the quality of the simulator training experience,” Dickinson noted.
CIS Sponsors In-House Accredited Training & Assessment
/in Company News, NCCER News, Resources /by Tracy BennettAs an NCCER sponsoring organization, Crane Industry Services, LLC (CIS) can help companies benefit from accreditation. In addition to sponsoring other crane and rigging training providers, CIS now sponsors Graycor Southern Inc. (GSI), a heavy industrial contractor based in Atlanta, Ga.
“Sponsorship was important to us,” says John Paul White, Graycor Southern’s director of safety. CIS’s expertise in training and qualifying trainers was important to White. “Not only did they ensure we comply with NCCER, but they also showed us the right way to do that training for our accreditation. You can’t ask for any better experience,” said White.
Under CIS’s NCCER sponsorship, companies have access to training and assessments backed by teams of Subject Matter Experts (SMEs). The NCCER programs are evaluated through the National Craft Assessment and Certification Program. NCCER’s crane operator certifications are ANSI accredited and OSHA recognized, which meets current compliance regulations.
As a sponsoring organization, CIS offers its clients cost savings and a long list of administrative benefits. Companies may train and assess their employees in more than 70 different craft and construction management areas. The process makes sense for contractors that specialize in building power plants, commercial buildings and government facilities.
Managing credentials can be quite labor intensive. “We handle their application for assessment, the reporting of assessment results, the processing of assessments, and verification of individual credentials for every person in their organization,” explains Debbie Dickinson, CEO of CIS. CIS also manages the auditing process, conducting an inventory of exams every 30 days and maintaining all records necessary for audit completion.
As a part of its NCCER sponsorship services, CIS works with the organization to train its in-house instructors. “We conduct an instructor certification program, and every candidate has to complete registration and application. We manage that process all the way to the cards in their wallet. We also track their individual credentials,” said Dickinson.
CIS carefully evaluates the companies it chooses to sponsor under NCCER. Dickinson says Graycor Southern Inc., is a company that is serious about achieving a quality, trained, and documented workforce. “One of the things that made us willing to sponsor Graycor Southern is their commitment to setting a safety culture. That’s a big investment on their part, and they’re serious about it. In addition, they invest in workforce development, and are a strong part of the community.”
In fact, White submitted to a battery of NCCER tests to experience what the entry-level craft professional would go through. “A little out of the ordinary” is how he describes his choice, “but we wanted to know if the NCCER training is worth what we think it’s going to be. If we’re going to put someone through the rigors, we’re going to go through them too, to gain an understanding of the full expectations and goal of the training,” he explains. “It gave us a better understanding of how to conduct the tests. That’s important to us.”
Dickinson appreciated White’s approach. “He put himself, as a leader, in the shoes of an employee at the most entry level. That’s the right message to send to your employees,” she says of White and Graycor.
CIS Launches New Communication Tool at ICUEE
/in Company News, Resources, Safety /by Tracy BennettTechnology and safety are compatible strategies that improve operations. Crane Industry Services, LLC (CIS) joins CM Labs Simulations at the International Construction & Utility Equipment Expo, Oct. 1-3, in Louisville, Ky.
Visitors to Booth 4358 can test-drive one of two Vortex® training simulators from CM Labs. Crane Industry Services deploys Vortex simulators at its Centered on Safety training center for crane operator training and qualification. “Simulators are a solid part of developing skilled workers. The ability to transfer skills learned on a simulator to actual machines makes simulator training an affordable way to maintain operator qualifications,” said Debbie Dickinson, CEO of CIS.
In addition, CIS will announce its newest assessment and communication tool titled, Leading Safety Works.© “Every project involves different workers, varying deadlines, and a long list of individual tasks. Leading Safety Works is a simple tool for identifying resources and safety strategy through the full project timeline. It also outlines instructions for how to handle unplanned occurrences,” says Dickinson.
According to Construction Industry Institute, accidents are most likely to occur during unplanned work. “One of the objectives of Leading Safety Works is to establish 90-day increments with clear plans for accountability, project goals, communication and most importantly, how jobs will be done well, safely, on time and in budget,” said Dickinson.
Project management and safety are never a one-size-fits-all concept. Project managers need a simple plan that embodies the company’s safety culture, as well as employee engagement and the non-negotiables associated with the job. “Then the result is a stronger, more profitable organization, with a reputation of integrity,” she said.
Business Partnerships Support Workforce Development
/in Company News /by Tracy BennettCompanies in construction and utility markets can launch successful workforce development initiatives by partnering with other businesses and area schools. Members of Southeastern Construction Owners and Associates Roundtable (SCOAR) are working together to do just that.
“Meeting discussions often turn to concerns over how to fill jobs with qualified workers and the future workforce,” said Debbie Dickinson, CEO of CIS, and a member of the SCOAR Workforce Development Committee. “The association fosters collaboration, and several member companies have taken the initiative to work toward increasing the qualified labor pool in the Southeast.”
Crane Industry Services, LLC is working together with representatives from utility construction company Graycor Southern Inc., Kennesaw, Ga., electrical substation constructor Aubrey Silvey, Carrollton, Ga., equipment rental provider United Rentals, and Bremen High School, Bremen, Ga.
“Often, school systems need assistance from industry to develop relevant skills-based craft training curriculum, but don’t know where to start,” said Dickinson. CIS recommended using NCCER Core Curriculum. Module 1 Basic Safety is similar to an OSHA 10-hour training. CIS staff instructor Noel Whelchel, who has a Georgia Teaching Certificate, will deliver this class. “I hope it encourages them to consider a career in a craft trade,” he said.
As part of the partnership, Graycor Southern’s Safety Director John Paul White and Vice President of Operations Shawn Buchanan visited Bremen High School. “In our discussions with students we demonstrated how working in craft trades is a viable career option,” said White. “Our goal was to show them there are paths for success besides college.”
White believes having construction-related businesses involved in a workforce development program at the middle- and high-school level is a great thing. “You can show the future of our country that construction companies are willing to invest in them as long as they are willing to put forth an effort.”
Workforce Development is a good investment for the industry and your community. Dickinson encourages other contractors, training providers, and equipment suppliers to launch workforce development programs with their local schools. Here are tips and suggestions:
Creating a Safety Culture begins with Authentic Leadership
/in Safety /by Tracy Bennett“Everyone wants a safe organization, but if you’re legitimately, authentically leading a focused safety initiative, you’ll know what’s going on in your organization,” says Debbie Dickinson, CEO of CIS. “Authentic safety leaders can specifically name the potential hazards in their organization, and recognize when a task is being performed correctly. Otherwise, how can leaders lead the charge for safety?” Dickinson subscribes to the thoughts of Don Maxwell who wrote, “a leader is one who knows the way, goes the way, and shows the way.” A company that follows this philosophy is set up to be a safe organization, in Dickinson‘s opinion.
“Imagine a powerline worker forgetting his insulated gloves in his truck or locker, or choosing not to wear them despite knowing wearing them is company policy. What behavior causes someone to make that decision?” poses Dickinson. “Is it apathy or a lack of fear of the repercussions? What causes people to believe that this company would not pay for an hour overtime for that worker to go back to his locker and get his insulated gloves?” Wearing safety gear should be a non-negotiable, says Dickinson. Ignoring the policy should have repercussions such as suspension without pay—so that employees know the company is serious about safety—as well as abundant rewards and praise for working safely. Instead of counting days without injuries, maintain high standards for safety and reward those who excel at maintaining them.
In the construction and utility industries, safety compliance is paramount to the success of the operation and the lives of the people working within it. Unfortunately, writes Krammer, there’s a vast difference between basic compliance and a true commitment to safety. While basic compliance often looks like simply meeting safety standards, a true commitment to safety arises when authentic leaders inspire engaged workers.
Here are CIS’ suggestions for engaging your employees in a safety culture.
“Leading from the inside-out requires connecting with your own values and leading from an authentic place. Remember that you, the leader, set the example to everyone who works for you, and you must teach or inspire other leaders to do the same,” writes Krammer. If you want a safe organization, as a safety leader you must chart the course and lead by example and knowledge. Leaders brave enough to take this charge have much to gain. Those who do not, have everything to lose.
Greg Brown Joins Crane Industry Services Staff as Crane Inspector and Trainer with Background in Entertainment Rigging
/in Company News /by Tracy BennettThere is a great need for equipment inspections in the entertainment industry, says Brandon Bowling, with United Rentals Sports & Entertainment Division. Bowling rents equipment such as high-reach forklifts and boom lifts to studios which rig cameras and lights to the machinery. He says safety is as crucial to the entertainment industry as it is to the construction sector. “All the major studios—Sony, Disney, Warner, Universal, Paramount—require inspection and extensive operator and rigger training. Studios do unbelievable special effects and stunt work. Cranes help get the job done. Before they do any of that, they have an inspection service like CIS go over the equipment and make sure every one of those people is qualified to do what they’re trying to do.”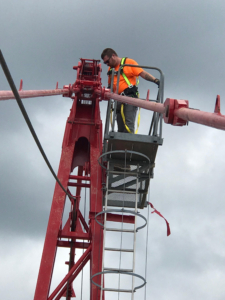
Brown is an NCCER-Certified Instructor, a Mobile Crane Examiner, an Assessment Coordinator, and a Curriculum Performance Evaluator. His background is in concert stage construction, and the similarities to vertical construction lie in the rigging involved, he says. “On the music side, you raise objects, like speakers and lights, and leave them there for the show. Then you bring them down. With cranes, you’re moving materials to where they’re needed on a job site or on a building. The rigging principles are much the same.”
If you would like to schedule training, or to have one of our qualified crane inspectors come to your place of business, contact Fred Robinson at 770-783-9292 or Fred@CraneIndustryServices.com. Greg is also available at Greg@CraneIndustryServices.com
CIS Demo Event Attendees Praise the Benefits of Training with a CM Labs Crane Simulator
/in Company News, Skilled Labor Supply /by Tracy BennettIn attendance were representatives from IUOE Local 926, Oak Ridge National Laboratory, the Georgia Department of Transportation, as well as regional and national construction and highway companies.
Since 2016, CIS has used a full-size simulator which is the forerunner to the Vortex Advantage, produced by CM Labs. The Vortex Advantage is an immersive training simulator with a plug-and-play training platform that is scalable to training needs and customizable to the crane fleet. In contrast, the new Vortex Edge Plus is designed for simple transport and set-up. “The desktop-style simulator is portable, making it easier for training organizations to bring simulator training to their clients’ locations,” said David Clark, content manager, CM Labs Simulators. “It is equipped to run any CM Labs training module, which includes mobile cranes, tower cranes, forklifts, and earthmoving equipment.”
“During the event, there was a lot of discussion about how expensive it is to train an operator,” said Dickinson. “With a simulator, one person can be trained much faster and more economically than in the cab of a crane.” The self-guided programs are progressive in nature, and capture operator metrics, for valuable feedback, explains Clark. CIS sends a simulator technician, who is also a certified instructor and certified crane operator, to set up the portable simulator in different locations. The instructor handles the technical side of the machine and can simultaneously coach the trainees. The simulator-based training reduces the man hours to train to a 3: or 4:1 ratio, and does not require job site supervisors or rigging crews for the training exercise, or valuable equipment time.
Demo event attendee Nathan Sauls, corporate health and safety director for Brooks Berry Haynie and Associates (BBH), an electrical contractor based in Mableton, Ga., said he can see many advantages to incorporating a simulator into crane operator training. For BBH, the biggest is in screening the qualifications of potential new hires. “I tried both the portable and permanent machines at the CIS event. I can see BBH, in the future, using that technology to set a baseline for hiring operators. It’s definitely got some good qualities for that purpose.”
He says it’s an expensive investment to hire personnel who may not have as much experience as they claim. Currently, BBH’s pre-hire screening involves comparing the skills of the potential employee to an operator they know is qualified. “It can be a financial drain if you spend money hiring someone and putting them in the field only to find out they’re not all they’re cracked up to be. With a simulator you can set a baseline on that good operator,” says Sauls.
Mark Templeton, business manager for the IUOE Local 926 in Rex, Ga., says training on the simulator is a realistic experience. “The motion, the seat moving around, giving you the effect of a real-life crane cab experience impressed me,” he said. “I’m a crane operator myself and the effect was realistic. We have a CM Labs simulator at the IUOE international training site and I’ve been able to get on it.” He believes the tabletop models are good for learning a crane’s functions, such as LMI readings, and better understanding the particular crane’s operations. “But the big system, that gives you the seat simulation, the movement and the motion, is dead on to what you’re going to get in the cab of a crane.”
A crane operator would pick up skills more quickly with a simulator, believes Templeton. “There are more things he can be aware of, and different skills that can be taught, in that situation,” he says, noting he’s spent 20 years in crane operations in the field and has worked around cranes of all types. “Your initial fears of being in a crane and the risks involved in operating heavy machinery—you take that risk factor out when you practice using a simulator, and you avoid the chance of damaging the equipment.”
Illustrating that point exactly, CIS reported that shortly after the CM Labs demo event, a customer utilized the cab-style simulator to prepare for a rough-terrain crane practical exam for crane operator certification. The operator had several months of job-related experience before starting the training. After spending about 40 hours on the Vortex simulator and 10 hours on an actual crane in the yard, the operator was able to pass the practical exam on the first try.
“Many trainees would require more time in the seat to pass the practical exam from the cab of a real crane, which further validates the quality of the simulator training experience,” Dickinson noted.